Saltar a un capítulo clave
Comprender las aleaciones de magnesio
Las aleaciones de magnesio ocupan un lugar único en el ámbito de la ciencia de los materiales. Al ser el más ligero de todos los materiales estructurales, su uso proporciona varias ventajas, al tiempo que sus propiedades se potencian con la aleación.
Lasaleaciones de magnesio son mezclas de magnesio con otros metales, a menudo aluminio, zinc, manganeso, silicio, cobre, etc., que mejoran la fuerza y la resistencia a la corrosión del metal primario: el magnesio.
Sus propiedades únicas las hacen cruciales para varios segmentos industriales, como los sectores automovilístico y aeroespacial, donde la reducción de peso es de suma importancia sin comprometer la resistencia y la durabilidad.
Definición de aleaciones de magnesio
El magnesio, el metal estructural más ligero, tiene aproximadamente un tercio de la densidad del aluminio. Las aleaciones de magnesio obtienen sus propiedades mejoradas aleando el magnesio con otros metales múltiples.
- Aleaciones forjadas destinadas a soportar una deformación plástica sustancial durante la fabricación.
- Aleaciones de fundición desarrolladas para aplicaciones que requieren formas intrincadas y complejas.
En ambos tipos, los elementos de aleación utilizados habitualmente incluyen aluminio, zinc, silicio, manganeso y otros.
Por ejemplo, la aleación AZ91D, una elección popular para la fundición a alta presión, se compone de un 9% de aluminio (A), un 1% de zinc (Z) y el 90% restante, de magnesio.
El comportamiento de estas aleaciones también puede mejorarse mediante tratamientos térmicos, como el recocido en solución y el envejecimiento, para conseguir las propiedades mecánicas deseadas.
Historia de las aleaciones de magnesio
Las aleaciones de magnesio han evolucionado considerablemente a lo largo del siglo pasado en función de las exigencias de las distintas industrias y ámbitos en los que se utilizan.
Una de las primeras aplicaciones conocidas de las aleaciones de magnesio fue en los dirigibles Zeppelin, a principios del siglo XX, con Elektron, nombre comercial de una serie de aleaciones de magnesio desarrolladas por una empresa alemana.
1910s | Se introdujo la aleación ZK60, de excelente resistencia. |
1950s | El uso de aleaciones en la industria aeroespacial cobró impulso. |
1990s | El CFRP empezó a sustituirla en la industria aeroespacial y en los coches de carreras. |
Importancia de las aleaciones de magnesio en la ingeniería
Las aleaciones de magnesio han ganado una enorme popularidad en aplicaciones de ingeniería, debido principalmente a su notable relación peso/resistencia, reciclabilidad y coste aceptable. Por ello, se están utilizando ampliamente en diversas áreas, como:
- Automoción: Se utilizan en piezas de automóviles para reducir el peso.
- Aeroespacial: Estructuras y piezas de aviones y naves espaciales.
- Electrónica de consumo: Carcasas de teléfonos móviles y ordenadores portátiles.
- Medicina: Implantes y dispositivos ortopédicos.
Su baja densidad, alta relación resistencia-peso, excelentes características de mecanizado y buena capacidad de amortiguación hacen que estas aleaciones sean muy adecuadas para estas aplicaciones.
Además, a medida que el mundo avanza hacia el desarrollo sostenible, la facilidad de reciclaje de las aleaciones de magnesio aumenta su campo de aplicación, lo que las convierte en un material de futuro en aplicaciones de ingeniería.
Propiedades de los materiales de aleación de magnesio
Las propiedades de las aleaciones de magnesio pueden clasificarse a grandes rasgos en características físicas y químicas. Ambos conjuntos de propiedades pueden influir enormemente en su funcionalidad y rendimiento en una amplia gama de aplicaciones. Esta diversidad de propiedades hace que las aleaciones sean cada vez más atractivas para ingenieros y diseñadores.
Propiedades físicas de las aleaciones de magnesio
Las aleaciones de magnesio poseen varias propiedades físicas que influyen en su utilidad en diversas aplicaciones. Estas propiedades físicas incluyen:
- Baja densidad: El magnesio es el metal estructural más ligero del mundo. Su ligereza lo convierte en una buena elección para aplicaciones en las que la reducción de peso es crucial, como la automoción, la industria aeroespacial y la electrónica portátil.
- Elevada relación resistencia-peso: Aunque el magnesio es ligero, presenta una resistencia significativa. Cuando se alea con otros metales, su resistencia aumenta, convirtiéndolo en un material robusto y fiable.
- Buena capacidad de amortiguación: Las aleaciones de magnesio poseen una gran capacidad de amortiguación, que es una medida de la resistencia al movimiento vibratorio u oscilatorio. Esta propiedad particular encuentra aplicaciones útiles en la industria automovilística y ferroviaria.
- Excelente maquinabilidad: Las aleaciones de magnesio son famosas por su maquinabilidad. Se pueden manipular con menos fuerza y, por tanto, consumen menos energía de fabricación.
La aleación desempeña un papel crucial en la mejora de las propiedades físicas del magnesio. Por ejemplo, la adición de aluminio al magnesio forma una aleación que posee una tendencia al agrietamiento por corrosión bajo tensión significativamente mejorada. Esta aleación, conocida como AZ91, es muy popular en aplicaciones de fundición a alta presión.
Propiedades químicas de las aleaciones de magnesio
Las aleaciones de magnesio, debido a su naturaleza química, presentan algunas propiedades características:
- Reactividad: Al ser un metal activo, el magnesio tiene una gran afinidad por el oxígeno, lo que lo hace susceptible a la oxidación. Para mitigar este problema, las aleaciones de magnesio suelen incorporar metales pesados como el níquel o elementos de tierras raras.
- Afinidad por el silicio: El magnesio muestra una considerable afinidad por el silicio. Esto es beneficioso, ya que conduce a la formación de capas de siliciuro de magnesio, que pueden impedir la difusión de especies corrosivas a la superficie del metal, mejorando así la resistencia a la corrosión.
Hay que tener en cuenta que las propiedades químicas de las aleaciones de magnesio pueden adaptarse aún más según los requisitos de la aplicación mediante técnicas de aleación y tratamiento térmico.
Resistencia a la corrosión de las aleaciones de magnesio
La resistencia a la corrosión es una consideración esencial cuando se trabaja con cualquier metal, y las aleaciones de magnesio no son una excepción. Las aleaciones de magnesio suelen ser más susceptibles a la corrosión que la mayoría de los demás metales, debido principalmente a su activo comportamiento electroquímico. Sin embargo, esto puede mitigarse mediante diversas técnicas.
Un método muy utilizado es el anodizado. Esta técnica utiliza procesos electroquímicos para crear una capa protectora de óxido sobre la superficie de las aleaciones de magnesio. Los tratamientos superficiales como el cromado, el fosfatado y el chapado también son eficaces para mejorar su resistencia a la corrosión.
Por ejemplo, la AZ31 es una aleación de magnesio que, tras tratamientos superficiales como el anodizado o el cromado, demuestra un aumento significativo de la resistencia a la corrosión.
Resistencia y durabilidad de las aleaciones de magnesio
Al hablar de resistencia y durabilidad de las aleaciones de magnesio, es importante saber que estos términos se refieren a la capacidad de un material para soportar las fuerzas aplicadas sin deformarse ni romperse.
El límite elástico de las aleaciones de magnesio depende en gran medida de los elementos de aleación y de su concentración. La resistencia a la tracción, que mide la resistencia de un metal a ser arrancado, de las aleaciones de magnesio suele oscilar entre 130 y 300 MPa. Su elevada relación resistencia-peso lo convierte en un candidato excelente para las industrias aeroespacial y del automóvil.
El límite elástico es la tensión a la que un material empieza a deformarse plásticamente.
Además, la durabilidad de las aleaciones de magnesio, es decir, su vida útil y su capacidad para soportar condiciones duras a lo largo del tiempo, aumenta con diversos tratamientos, como el trabajo en caliente, el trabajo en frío y los tratamientos térmicos (como el recocido por disolución y el endurecimiento por precipitación).
Tipos de aleaciones de magnesio
Aunque las aleaciones de magnesio son versátiles, pueden clasificarse específicamente en función de sus propiedades mejoradas. Hay varios tipos agrupados principalmente como aleaciones de magnesio de alta resistencia, aleaciones de magnesio resistentes a la corrosión y aleaciones de magnesio resistentes al calor.
Aleaciones de magnesio de alta resistencia
En el ámbito de las aleaciones de magnesio, algunas variantes se diseñaron específicamente para ofrecer una mayor resistencia. Estas aleaciones de magnesio de alta resistencia suelen reforzarse con elementos como aluminio, zinc o elementos de tierras raras. En comparación con las aleaciones de magnesio estándar, estas variantes de alta resistencia presentan una mayor durabilidad bajo tensión mecánica, lo que las hace ideales para aplicaciones estructurales en las que la estabilidad es crucial.
Una aleación de magnesio de alta resistencia muy utilizada es la AZ91. Compuesta por un 9% de aluminio y un 1% de zinc, y el resto de magnesio, la AZ91 es famosa por su excepcional dureza y resistencia al impacto. Y lo que es más importante, el aluminio aumenta la resistencia, mientras que el zinc garantiza una buena resistencia a la corrosión por intersticios.
Algunas aleaciones de magnesio de alta resistencia se refuerzan con elementos de tierras raras como el itrio. Una de estas aleaciones es la WE43, que consiste en itrio, elementos de tierras raras pesadas y circonio. La presencia de estos elementos eleva sustancialmente la resistencia de la aleación incluso a temperaturas elevadas. Del mismo modo, la ZK60 es otra aleación superior de magnesio de alta resistencia, está constituida por zinc y circonio y ha demostrado una excelente resistencia y ductilidad.
Aleaciones de magnesio resistentes a la corrosión
Aunque las aleaciones de magnesio tienden intrínsecamente a ser más susceptibles a la corrosión, mediante un cuidadoso diseño de la aleación y procesos de tratamiento térmico, se han conseguido aleaciones de magnesio resistentes a la corrosión. Estas aleaciones consiguen ralentizar o evitar la corrosión incluso cuando se exponen a ambientes salinos, ácidos o húmedos.
La forma más eficaz de mejorar la resistencia a la corrosión de las aleaciones de magnesio es aleándolas con elementos que tengan una mayor resistencia natural a la corrosión, especialmente aluminio, manganeso y elementos de tierras raras. Por ejemplo, la AM60, compuesta principalmente de magnesio, con un 6% de aluminio y una traza de manganeso, es conocida por su buena resistencia a la corrosión, ductilidad y excelente colabilidad.
Otra aleación notable de alta resistencia a la corrosión es la AE44, constituida por un 4% de aluminio y elementos de tierras raras. Esta aleación se utiliza predominantemente en aplicaciones de automoción por su mayor resistencia a la corrosión y su alto rendimiento a temperaturas elevadas.
También se han utilizado ampliamente diversos tratamientos superficiales para mejorar la resistencia a la corrosión de las aleaciones de magnesio. El sellado, la anodización y el cromado son algunos de ellos, que forman una capa impermeable de óxido de magnesio en la superficie de la aleación que impide el proceso de corrosión.
Aleaciones de magnesio resistentes al calor
Las aleaciones de magnesio resistentes al calor son una clase específica de aleaciones capaces de mantener sus propiedades incluso a altas temperaturas. Son cada vez más importantes en entornos en los que el estrés térmico es habitual, como motores, líneas de transmisión eléctrica y aviones de alta velocidad.
La adición de elementos de aleación específicos como aluminio, zinc, estroncio y elementos de tierras raras es el enfoque habitual para formular aleaciones de magnesio resistentes al calor. Por ejemplo, la AS41, compuesta principalmente de magnesio con un 4% de aluminio y un 1% de silicio, es una aleación que muestra una mayor resistencia a las altas temperaturas.
Una serie de aleaciones con un alto contenido de elementos de tierras raras, QE22, WE43 y EV31A, también son conocidas por su excelente rendimiento a altas temperaturas. Se considera que la QE22 tiene una de las mayores resistencias a la fluencia entre las aleaciones de magnesio, lo que la convierte en una opción perfecta para las cadenas cinemáticas y los turbocompresores de los vehículos.
Hay que tener en cuenta que la resistencia térmica de estas aleaciones también depende en gran medida de sus procesos de tratamiento térmico. Procesos como el recocido por disolución, el temple y el endurecimiento por envejecimiento pueden desempeñar un papel fundamental en el aumento de la resistencia térmica de las aleaciones de magnesio.
Ventajas de las aleaciones de magnesio
Las aleaciones de magnesio, al tener propiedades físicas y químicas únicas, ofrecen una serie de ventajas en aplicaciones de ingeniería. Los propios atributos que caracterizan a estas aleaciones, como su naturaleza ligera, su elevada relación resistencia-peso y su rentabilidad, se traducen en su importante potencial en diversos sectores industriales, especialmente en aplicaciones de automoción, aeroespaciales y electrónicas.
Naturaleza ligera de las aleaciones de magnesio
El magnesio es el más ligero de todos los metales estructurales, lo que hace que las aleaciones de magnesio sean excepcionalmente ligeras. Esta característica tiene una profunda influencia en numerosas aplicaciones, principalmente en industrias sensibles al peso, como la aeroespacial y la automovilística.
La industria aeroespacial se esfuerza constantemente por reducir el peso de los componentes para mejorar la eficacia de los vuelos. La naturaleza ligera de las aleaciones de magnesio permite reducir considerablemente el peso de diversas piezas de los aviones, lo que, a su vez, conlleva una mayor eficiencia en el consumo de combustible y una reducción de las emisiones. Del mismo modo, en la industria del automóvil, los vehículos ligeros tienen mejor aceleración, mejor frenado y mayor eficiencia de combustible. Como resultado, al sustituir los componentes pesados de acero por aleaciones ligeras de magnesio, los fabricantes pueden aumentar significativamente la eficiencia y el rendimiento de los vehículos.
Las aleaciones de magnesio también desempeñan un papel decisivo en la electrónica portátil, donde el peso es una preocupación crucial. Desde la carcasa de los teléfonos inteligentes hasta el cuerpo de los ordenadores portátiles, la baja densidad de las aleaciones de magnesio ayuda a mantener el peso de estos dispositivos al mínimo sin comprometer su resistencia y durabilidad.
La elevada relación resistencia-peso de las aleaciones de magnesio
A pesar de su ligereza, las aleaciones de magnesio presentan una elevada relación resistencia-peso. Esta propiedad mide la resistencia del material -definida por los límites de tensión antes del límite elástico y la fractura- frente a su peso. Matemáticamente, la relación resistencia-peso se calcula generalmente como el límite elástico dividido por su densidad:
\[\text{Relación resistencia-peso} = \frac{text{Rendimiento}} {{text{Densidad}}]Esta elevada relación resistencia-peso hace que las aleaciones de magnesio sean la opción preferida para aplicaciones que requieren robustez y compacidad. Debido a su capacidad para soportar grandes tensiones manteniendo la ligereza, estas aleaciones son perfectas para crear piezas duraderas y de alto rendimiento, desde bloques de motor de automóviles a cuadros de bicicleta e incluso chalecos antibalas.
Las aleaciones de magnesio ofrecen una robustez comparable a la del acero y el aluminio, al tiempo que son sustancialmente más ligeras. Esto les confiere una ventaja en sectores en los que se busca tanto la reducción de peso como la durabilidad, como el automovilístico y el aeroespacial. Por ejemplo, en aplicaciones de automoción, el uso de piezas de aleación de magnesio, como bloques de motor o paneles de carrocería, no sólo puede reducir el peso del vehículo, sino también mejorar sus prestaciones y aumentar su vida útil.
Rentabilidad de las aleaciones de magnesio
Las ventajas económicas de las aleaciones de magnesio suelen ser tan atractivas como sus propiedades físicas y químicas. En primer lugar, el magnesio es el octavo elemento más abundante en la Tierra y está fácilmente disponible, lo que lo convierte en una opción más económica que los metales más raros.
Además, las aleaciones de magnesio ofrecen una excelente maquinabilidad, lo que significa que pueden moldearse y trabajarse fácilmente. Esto reduce los costes de procesamiento, como los asociados al corte, taladrado y moldeado, con lo que el proceso global de fabricación resulta más rentable.
La durabilidad y larga vida útil de las aleaciones de magnesio también contribuyen al ahorro de costes. Debido a su mayor resistencia al desgaste, las piezas fabricadas con estas aleaciones suelen tener una vida útil más larga, lo que reduce la necesidad de sustituciones frecuentes y los costes de mantenimiento asociados.
Por último, en industrias como la automovilística y la aeroespacial, el ahorro de combustible resultante de la reducción de peso hace que las aleaciones de magnesio sean una solución más rentable a lo largo de la vida útil del vehículo o la aeronave. Por tanto, aunque el coste inicial de las aleaciones de magnesio puede ser superior al de algunos materiales tradicionales, la rentabilidad global suele ser superior si se consideran los costes totales del ciclo de vida.
Desventajas de las aleaciones de magnesio
Aunque las aleaciones de magnesio son célebres por sus numerosas ventajas, es imprescindible tener en cuenta sus inconvenientes, que pueden limitar su aplicación en determinados campos. Los principales retos a los que se enfrentan las aleaciones de magnesio giran en torno a su vulnerabilidad a la corrosión, su alta inflamabilidad y sus posibles limitaciones en entornos de altas temperaturas.
Vulnerabilidad a la corrosión de las aleaciones de magnesio
Una de las limitaciones significativas de las aleaciones de magnesio reside en su predisposición a la corrosión. La corrosión es un proceso natural que convierte un metal refinado en una forma químicamente más estable, como óxido, hidróxido o sulfuro. Como el magnesio es muy reactivo, sus aleaciones son propensas a la corrosión cuando se exponen a condiciones duras, especialmente en ambientes marinos y ácidos.
Esta alta reactividad del magnesio se debe a su posición en la serie galvánica, donde se encuentra en el extremo como metal más activo. La serie galvánica clasifica los metales en función de su reactividad electroquímica y su tendencia a corroerse, siendo los de la parte superior los menos corrosivos y los de la parte inferior los más corrosivos. Como las aleaciones de magnesio se sitúan en el extremo inferior de la serie, son más propensas a perder electrones durante su exposición a ambientes corrosivos, lo que provoca corrosión.
Serie galvánica: Lista que clasifica los metales según su reactividad electroquímica en un entorno de agua de mar.
Entre las formas frecuentes de corrosión que se observan en las aleaciones de magnesio están la corrosión galvánica, la corrosión por grietas y la corrosión por picaduras. La corrosión galvánica se produce cuando una aleación de magnesio está en contacto eléctrico con un metal noble superior, y ambos están sumergidos en un fluido conductor. Debido a la mayor reactividad del magnesio, éste se corroe preferentemente, mientras que el metal noble queda protegido. La corrosión por intersticios es una forma localizada de corrosión que suele producirse en el interior de pequeñas grietas o huecos donde puede acumularse una solución estancada. La corrosión por picaduras se manifiesta en forma de pequeñas picaduras similares a agujeros de alfiler en la superficie de la aleación de magnesio, que a menudo provocan fallos bajo carga.
Aunque se han propuesto varias soluciones potenciales para mitigar la corrosión en las aleaciones de magnesio, cada una tiene su propio conjunto de retos. Por un lado, la aleación con elementos como elementos de tierras raras, aluminio y zinc puede mejorar la resistencia a la corrosión, pero también encarece la aleación. Por otro lado, los revestimientos protectores pueden ralentizar considerablemente la corrosión, pero también pueden introducir otros problemas, como la posible contaminación durante la aplicación del revestimiento o el eventual desgaste de la capa protectora.
Alta inflamabilidad de las aleaciones de magnesio
Otro inconveniente notable de las aleaciones de magnesio es que son muy inflamables. Se sabe que el magnesio, al ser un elemento reactivo, entra en combustión a temperaturas relativamente bajas. Esto significa que en entornos donde la temperatura puede elevarse por encima de la temperatura de ignición del magnesio de \( 473^{circ}\, \mathrm{C} \) , también conocida como punto de inflamación, existe riesgo de incendio.
La combustión del magnesio da lugar a llamas intensas, brillantes y blancas, difíciles de extinguir con agua o dióxido de carbono, lo que hace que los incendios de magnesio sean peligrosamente persistentes. Por eso, para hacer frente a incidentes de incendio con aleaciones de magnesio hay que tomar precauciones especiales. La arena, el polvo químico seco o un extintor especial de clase D son los agentes extintores preferidos para los incendios de magnesio.
Un ejemplo clásico de riesgo de incendio con aleaciones de magnesio es el incendio de un coche. Si se incendia un coche con componentes de aleación de magnesio, la alta temperatura del fuego puede provocar la ignición de las piezas de magnesio. Esto puede provocar una reacción intensa y explosiva, extendiendo aún más el incendio y complicando los esfuerzos de los bomberos.
A pesar de los riesgos asociados, las aleaciones de magnesio se siguen utilizando ampliamente en diversas aplicaciones debido a sus ventajosas propiedades. Sin embargo, su inflamabilidad exige una manipulación cuidadosa y precauciones de seguridad específicas, sobre todo durante las fases de fabricación, almacenamiento y eliminación.
Límites de las aleaciones de magnesio en entornos de alta temperatura
A altas temperaturas, las aleaciones de magnesio presentan propiedades mecánicas reducidas, lo que podría limitar sus aplicaciones. El rendimiento reducido incluye una menor resistencia a la tracción y propiedades físicas alteradas, que pueden afectar negativamente a su funcionalidad en un entorno de alta temperatura.
Otro reto del empleo de aleaciones de magnesio a temperaturas elevadas es su degradación potencial debida a la oxidación progresiva del magnesio. A altas temperaturas, el magnesio de la aleación reacciona con el oxígeno del entorno para formar óxido de magnesio, un proceso denominado oxidación. Esta oxidación conduce a la formación de una capa quebradiza y no protectora de óxido de magnesio en la superficie de la aleación, que puede provocar fracturas y la consiguiente reducción de la integridad estructural.
También hay que mencionar que, debido al elevado coeficiente de dilatación térmica del magnesio, las piezas fabricadas con sus aleaciones pueden cambiar dimensionalmente cuando se someten a cambios de temperatura importantes. Esta falta de estabilidad dimensional puede ser un inconveniente en aplicaciones de alta precisión, donde la tolerancia dimensional es crítica.
Quienes pretenden utilizar aleaciones de magnesio en aplicaciones de alta temperatura suelen recurrir a la aleación con elementos que mejoran la tolerancia térmica. Por ejemplo, alear magnesio con elementos como aluminio, zinc y elementos de tierras raras puede mejorar su estabilidad térmica y aumentar su resistencia a la fluencia. Sin embargo, al hacerlo a menudo se produce una compensación con otras propiedades como la ductilidad y la tenacidad a la fractura. Por lo tanto, encontrar el equilibrio adecuado entre el rendimiento a alta temperatura y otras propiedades deseadas es crucial a la hora de diseñar aleaciones de magnesio para aplicaciones de alta temperatura.
Aplicaciones de las aleaciones de magnesio
Las aleaciones de magnesio se mantienen como una opción atractiva para diversas aplicaciones en distintos sectores. Este atractivo se atribuye a sus impresionantes propiedades, como su baja densidad, su excelente relación resistencia-peso y sus buenas características de mecanizado.
Las aleaciones de magnesio en la industria del automóvil
Las aleaciones de magnesio se han ganado un lugar en la industria del automóvil por su elevada relación resistencia-peso y su baja densidad. La producción de vehículos más ligeros es un objetivo de la mayoría de las empresas automovilísticas, ya que reducir el peso de un vehículo conlleva una mayor eficiencia de combustible, menos emisiones y un mejor rendimiento.
En la industria del automóvil, las aleaciones de magnesio se utilizan en diversas aplicaciones, como:- Motores de automóviles: Se utilizan en la fabricación de bloques de motor debido a sus excelentes propiedades de disipación del calor. La baja densidad de estas aleaciones hace que los motores sean más ligeros, lo que contribuye a la eficiencia general del combustible de los vehículos.
- Volantes: Las aleaciones se utilizan para fabricar volantes por su gran resistencia a los impactos.
- Cajas de transmisión: La excelente moldeabilidad y estabilidad dimensional de estas aleaciones las hacen ideales para cajas de transmisión.
El Grupo Volkswagen, uno de los principales fabricantes de automóviles del mundo, utiliza aleaciones de magnesio para sus cajas de transmisión. Esto ha supuesto una reducción de peso aproximada del 30% en comparación con las carcasas de transmisión tradicionales de aleación de aluminio. Estas aplicaciones demuestran el potencial transformador de las aleaciones de magnesio en la industria del automóvil.
Uso de aleaciones de magnesio en la ingeniería aeroespacial
La industria aeroespacial presenta una de las aplicaciones más exigentes para las aleaciones de magnesio. Con la creciente necesidad de materiales ligeros que puedan soportar las condiciones extremas que se experimentan en vuelo, las aleaciones de magnesio han demostrado ser una elección acertada.
Ingeniería aeroespacial: Este campo de la ingeniería gira en torno al diseño, desarrollo, ensayo y producción de aeronaves y sistemas relacionados. El uso de materiales ligeros y resistentes, como las aleaciones de magnesio, es crucial en esta industria.
- Estructuras aeronáuticas: Se utilizan en la construcción de armazones y componentes estructurales de los aviones debido a su excelente relación resistencia-peso y a sus buenas características de absorción de impactos.
- Piezas de motor: Dadas sus buenas propiedades de disipación del calor, las aleaciones de magnesio son eficaces en piezas de motores.
- Componentes interiores: Su gran estabilidad dimensional y facilidad de mecanizado las hacen perfectas para componentes interiores como las estructuras de los asientos.
Las aleaciones de magnesio en la electrónica y los dispositivos móviles
Las aleaciones de magnesio son una opción excelente en la industria electrónica y de dispositivos móviles, donde la demanda de materiales ligeros, compactos y de alto rendimiento es cada vez mayor. Estas aleaciones son especialmente apreciadas por su baja densidad, alta resistencia, excelente apantallamiento electromagnético y buena maquinabilidad, lo que las hace perfectas para aplicaciones como armazones de ordenadores portátiles, carcasas de teléfonos móviles y cuerpos de cámaras.
Se sabe que la serie de portátiles AG de LG utiliza una aleación de magnesio para la carcasa del portátil. Este uso de la aleación de magnesio contribuye a un diseño elegante, un peso más ligero y una mejor disipación del calor, mejorando así la experiencia del usuario.
Aleaciones de magnesio - Aspectos clave
- Entre los métodos para mejorar la resistencia a la corrosión de las aleaciones de magnesio están el anodizado, el cromado, el fosfatado y el chapado, que en conjunto crean una capa protectora de óxido sobre la superficie de la aleación.
- La resistencia de las aleaciones de magnesio varía en función de los elementos de aleación y su concentración; el límite elástico suele oscilar entre 130 y 300 MPa, lo que lo convierte en un material excelente en las industrias aeroespacial y automovilística por su elevada relación resistencia-peso.
- Las aleaciones de magnesio pueden clasificarse en tipos de alta resistencia, resistentes a la corrosión y resistentes al calor, cada uno de ellos desarrollado según sus aplicaciones y características específicas.
- Las aleaciones de magnesio, a pesar de ser ligeras, tienen una elevada relación resistencia-peso y son rentables, lo que las hace ideales para aplicaciones de automoción, aeroespaciales y electrónicas.
- Las desventajas de las aleaciones de magnesio incluyen su susceptibilidad a la corrosión, su alta inflamabilidad y sus limitaciones en entornos de alta temperatura.
Aprende más rápido con las 12 tarjetas sobre Aleaciones de magnesio
Regístrate gratis para acceder a todas nuestras tarjetas.
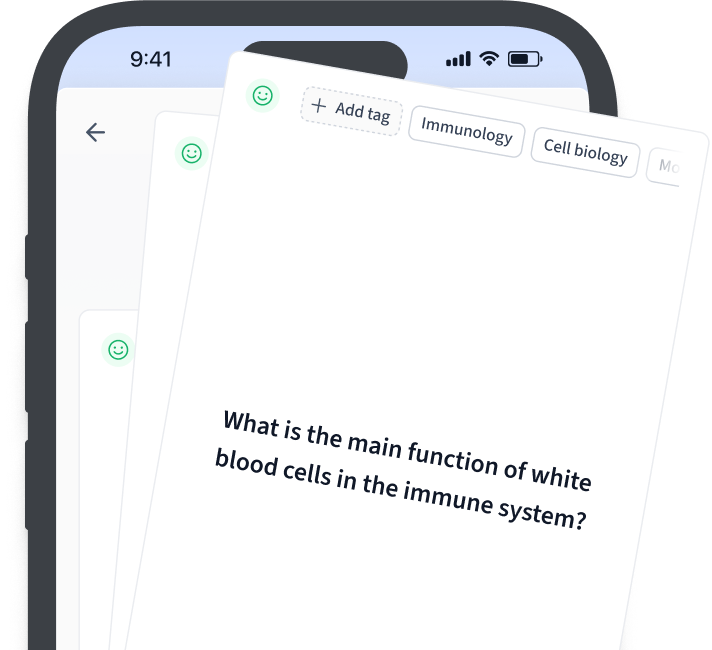
Preguntas frecuentes sobre Aleaciones de magnesio

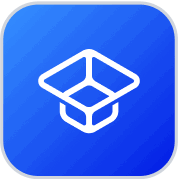
Acerca de StudySmarter
StudySmarter es una compañía de tecnología educativa reconocida a nivel mundial, que ofrece una plataforma de aprendizaje integral diseñada para estudiantes de todas las edades y niveles educativos. Nuestra plataforma proporciona apoyo en el aprendizaje para una amplia gama de asignaturas, incluidas las STEM, Ciencias Sociales e Idiomas, y también ayuda a los estudiantes a dominar con éxito diversos exámenes y pruebas en todo el mundo, como GCSE, A Level, SAT, ACT, Abitur y más. Ofrecemos una extensa biblioteca de materiales de aprendizaje, incluidas tarjetas didácticas interactivas, soluciones completas de libros de texto y explicaciones detalladas. La tecnología avanzada y las herramientas que proporcionamos ayudan a los estudiantes a crear sus propios materiales de aprendizaje. El contenido de StudySmarter no solo es verificado por expertos, sino que también se actualiza regularmente para garantizar su precisión y relevancia.
Aprende más